UCPath is getting a new look! Here’s what to expect, including downtime.
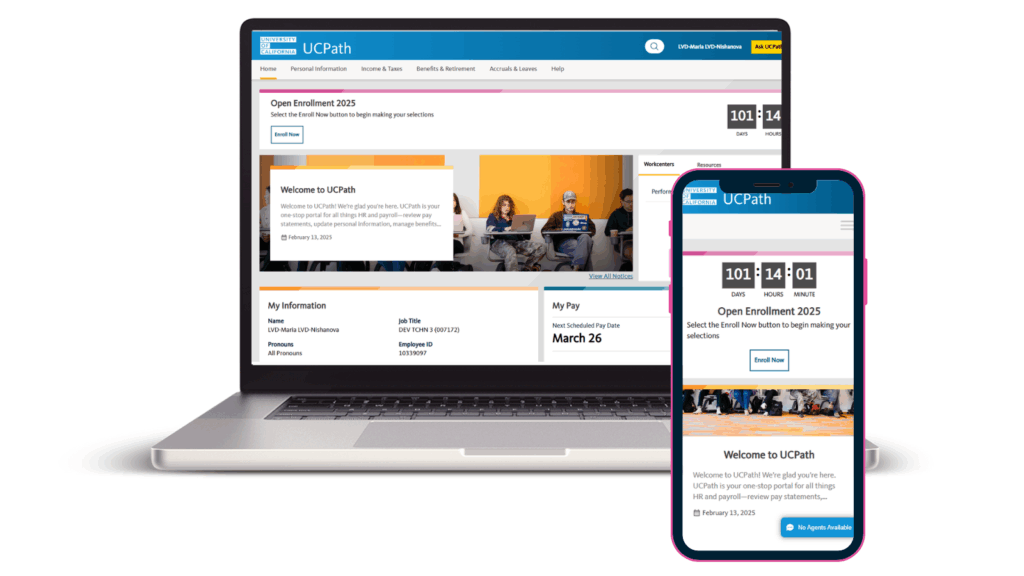
July 7, 2025
UCPath’s refreshed layout, improved navigation and responsive design will make it easier than ever to access and update your information.
Council of UC Staff Assemblies shares spring quarterly meeting update
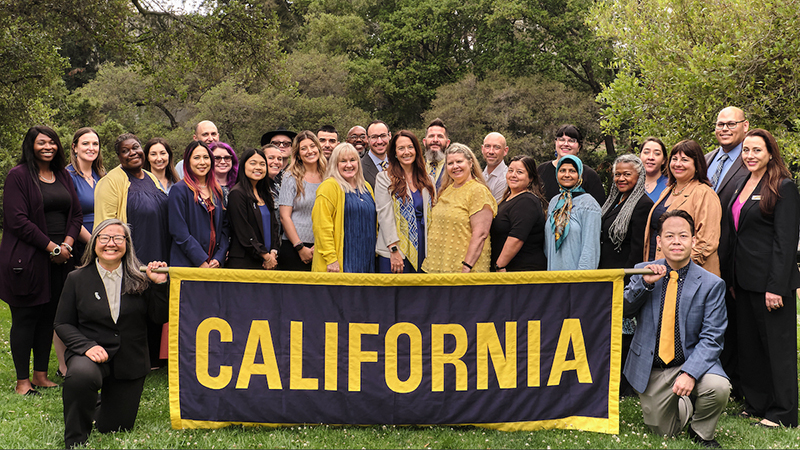
July 7, 2025
CUCSA’s spring meeting featured conversations with UC leaders, workgroup presentations and updates on matters of interest for UC staff.
Wondering if that ‘financial adviser’ is trustworthy? Read this.
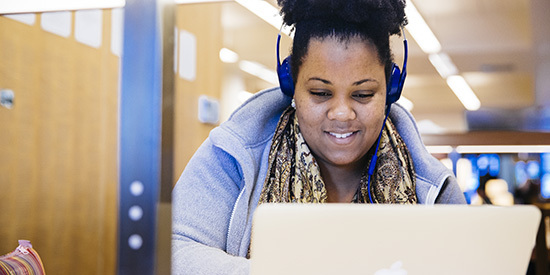
July 3, 2025
It’s easy to confuse unauthorized advisers with UC-contracted financial planning services.
Advisory for non-essential travel within the Middle East North Africa (MENA) Region
July 3, 2025
Updated travel advisory for the MENA Region issued on July 3, 2025, by Nathan Brostrom, Executive Vice President and CFO, and Kevin Confetti, Associate Vice President & Chief …
The University of California mourns the passing of former UC President Robert C. Dynes
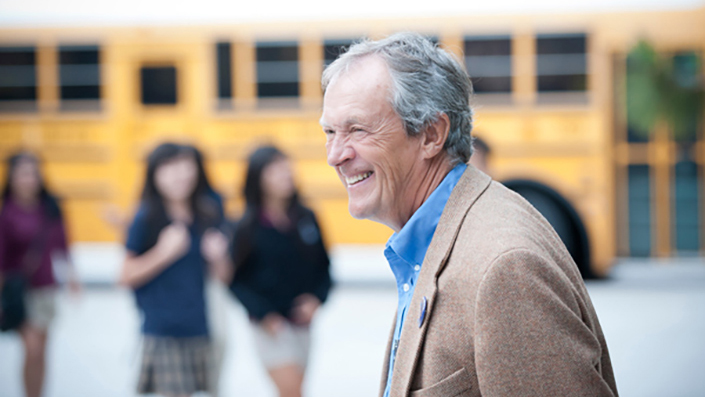
July 2, 2025
The UC community is deeply saddened by the passing of former UC President and former UC San Diego Chancellor Robert C. Dynes.
UC Tech Awards 2025 showcase courage and boldness in transforming UC technology
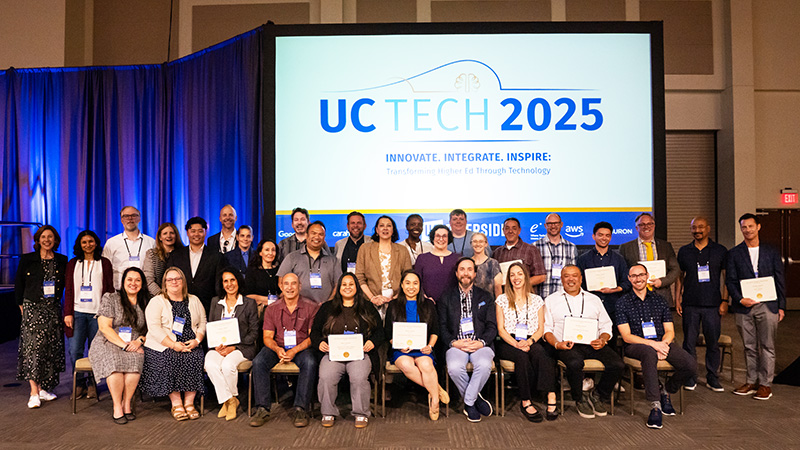
June 30, 2025
On June 26, UC honored two individuals and 12 teams from throughout the system with 2025 UC Tech Awards for technological advancement.
Register for CUCSA’s July 8 town hall
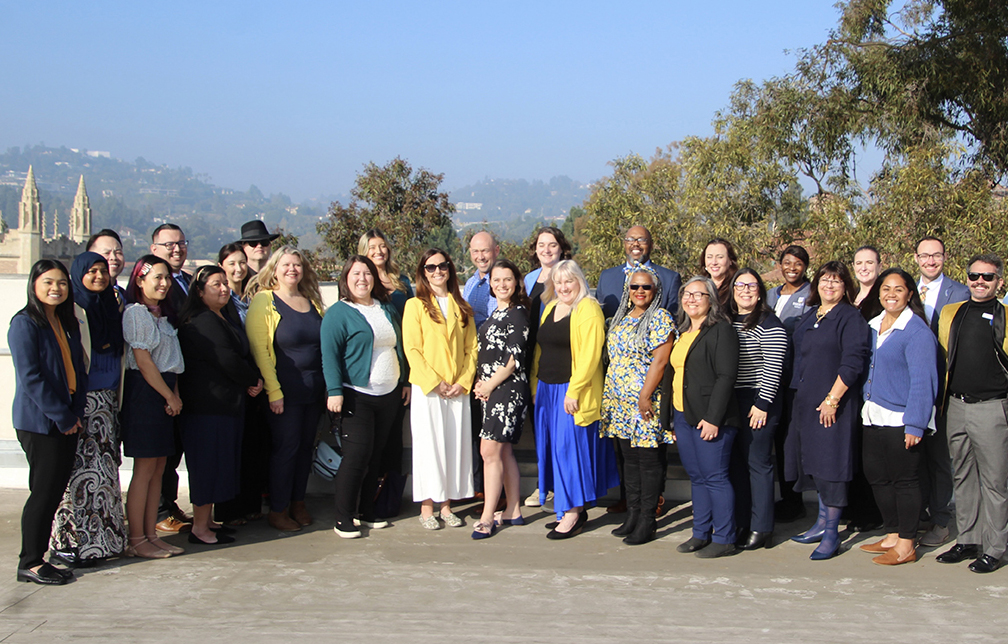
June 26, 2025
Join the Council of UC Staff Assemblies for a town hall featuring 2024-2025 workgroup reports and recommendations.
UC People: Ashfia Huq, nanoscience catalyst
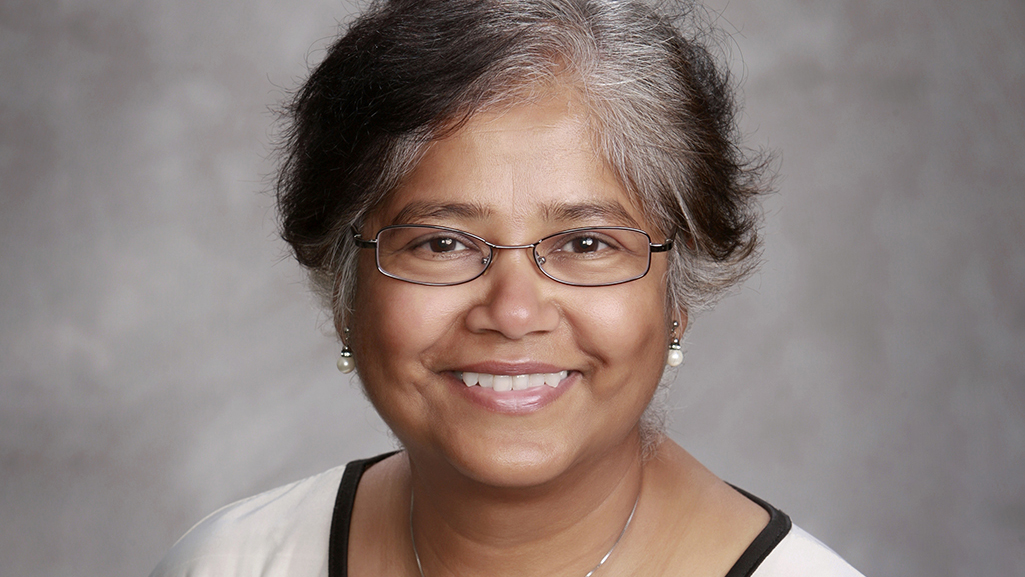
June 25, 2025
Ashfia Huq, director of the Molecular Foundry at Lawrence Berkeley National Lab, discusses the Foundry’s mission, capabilities and groundbreaking research.
First-ever UC Cooperative Extension Tribal Extension Office opens
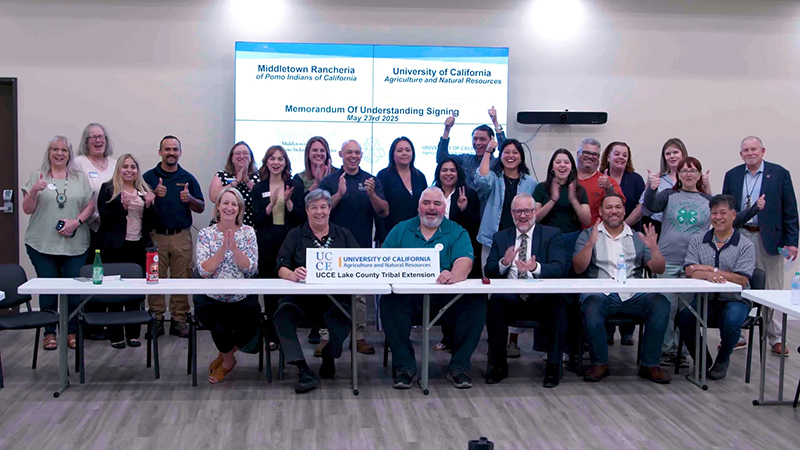
June 24, 2025
The Middletown Rancheria of Pomo Indians of California and UC Agriculture and Natural Resources have created a UCCE Tribal Extension Office.
UCOP employee resource group gives back on Memorial Day
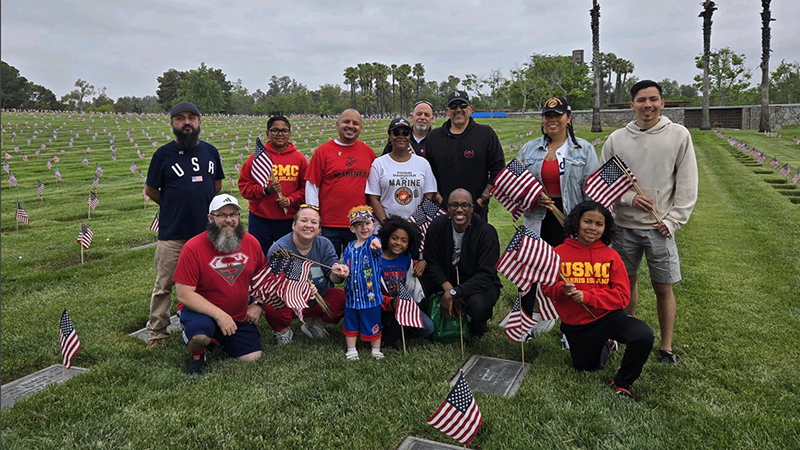
June 24, 2025
Veterans Among US gathered members, their families and their friends together to honor the lives of local deceased service members.